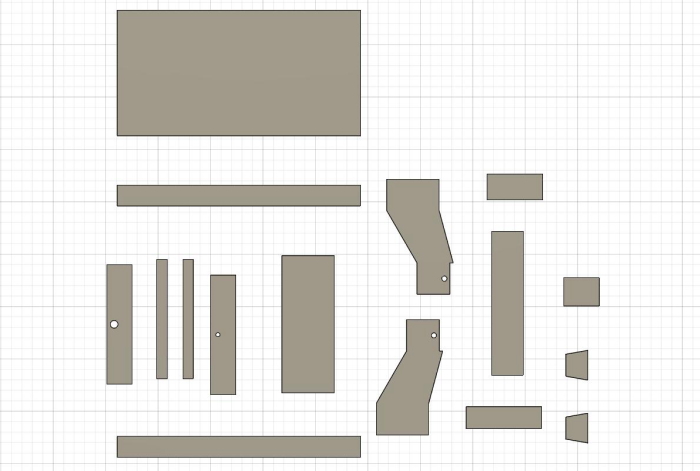 |
新しい年がまたやってきた。
2020年、今年も色々な物を作ろう。
と言うわけで、まずはCNC加工機のフレームの材料を発注した。
構成はシンプルなので部品点数は少ない。
材質はAL2017、いわゆる17Sと呼ばれる強度の高いジュラルミンです。
材料の厚みは15mmとした。フレームの厚みとしては十分と考えているが、実働させてもし強度が足りないようなら、厚みの変更はいつでも可能なのが自社開発の強みである。
一番大きなパーツは天板で、加工面の台となる部分。
このパーツのみ、厚みは5mmで設計した。理由は幾つか有るが、フレーム構成がいわゆる目の字なので、中間部分で凹むようなたわみは想定していない。
天板の上にMDFなどの加工用ベッドを設置するつもりなので、それらの表面加工はこのCNC機が自ら行います。
この材料が入荷したらいよいよCNC加工機の本体の製作に取り掛かります。 |
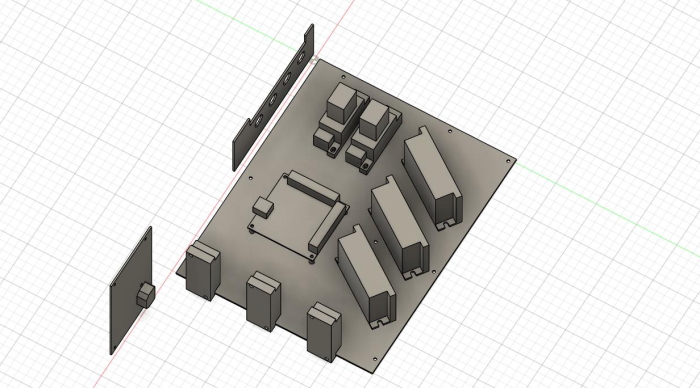 |
本体の材料が届くのを待つ間に、制御ボックスの設計をしています。
BOXその物は自作PC用に販売されているATXケースを使用します。
そして、マザーボードと同じサイズで製作した板に、各制御部品を設置することでスッキリとした仕上がりを目指します。
写真では少し判りにくいですが、横に倒したPCケースを斜め上から見た視点です。
斜めに3つ配置された部品は、ステッパーモーターのドライバーです。
なぜ斜めに配置しているかと言うと、PCケースに取り付けてある冷却ファンの風の流れが、ドライバーの表面のヒートシンクに効率よく吹き付けられるように角度を持たせ、各部を冷却後にケース後方の排気ファンから外部へと排気させる事で、冷却効率の高いエアーフローを実現させる為です。
これらのパーツ配置は配線の取り回しも考えに入れて行い、仕上がりの確かな物を目指します。
ここからマザー板やコネクター取り出し板(穴が4つ空いた板)、電源コネクター付きバックプレートをレーザー加工機で切り出します。
板の材質は2mmのアクリル板を使用。 |
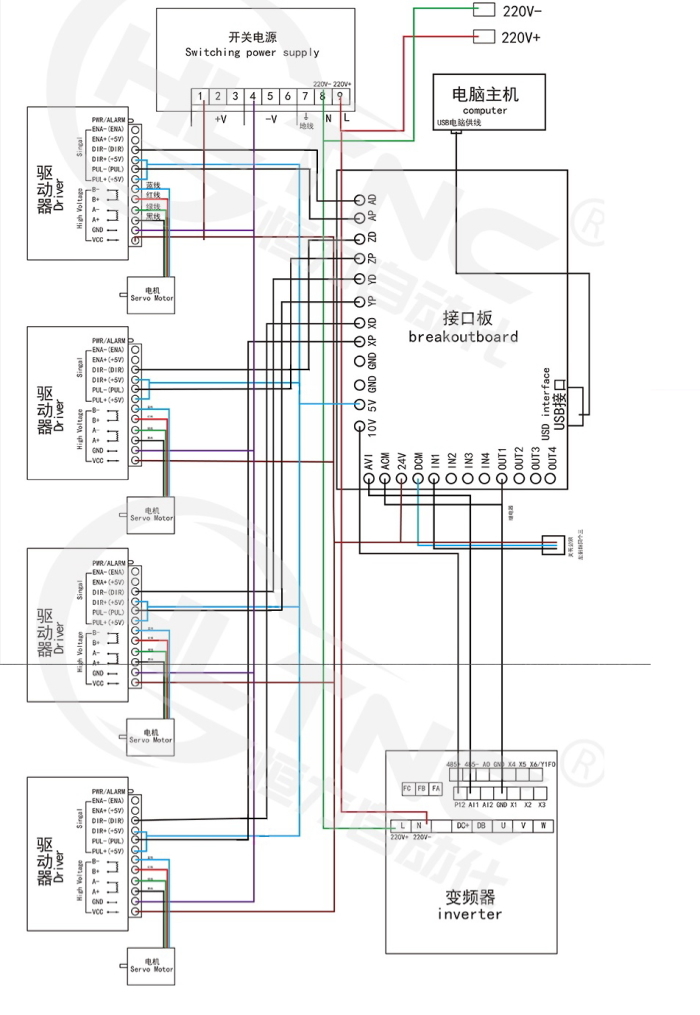 |
以前、その1のページで書いたが、メーカーのwebで紹介されている配線図の通りに配線しても動かない。
机上実験で動作させるまでに相当苦労しましたが、左の配線が正しい配線図です。間違えている部分を修正して、正しく動くように書き直して有ります。
この配線図が誰かの役に立つのかはわかりませんが、私の作業がこの後に制御Boxの組み込みに進む為、自分でも正確な配線図が必要なので、ここに載せておきます。
因みに私の環境では、この配線図で動きましたよと言うことです。 |
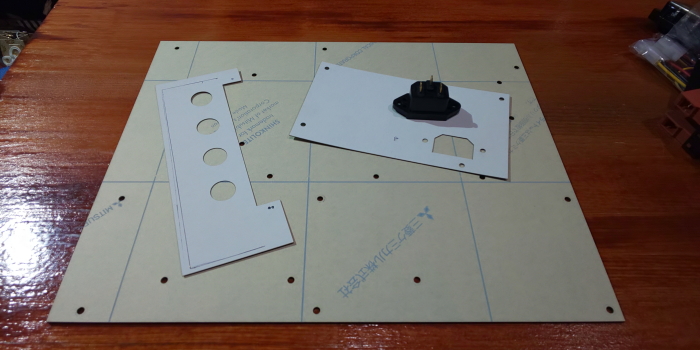 |
正月の間にCADで各部品を描いていて、今日レーザー加工機でテストカットしてみました。一番大きいのはATXマザーサイズのアクリル板です。
マザーは寸法が正確に描けている為、本番アクリルでカットしています。
他の二枚は寸法他、多少の手直しが考えられるので厚紙でテストカットします。この方法だと部品の嵌め合いや、ネジ穴の位置の微妙なずれの修正が可能なので良くやる手法です。
右の電源パネルは合格。電源ケーブル受けのソケットもばっちり適合しています。左のコネクター取出しは、ネジ穴の位置が確定出来なかったのを、現物合わせでネジ位置を型紙にマークして、再度採寸しCADに落とし込んで仕上げます。
この様にして各部のデザインを確かな物に仕上げて行きます。
後はUSBのソケットもコネクターの下に合わせたいので部品待ち。 |
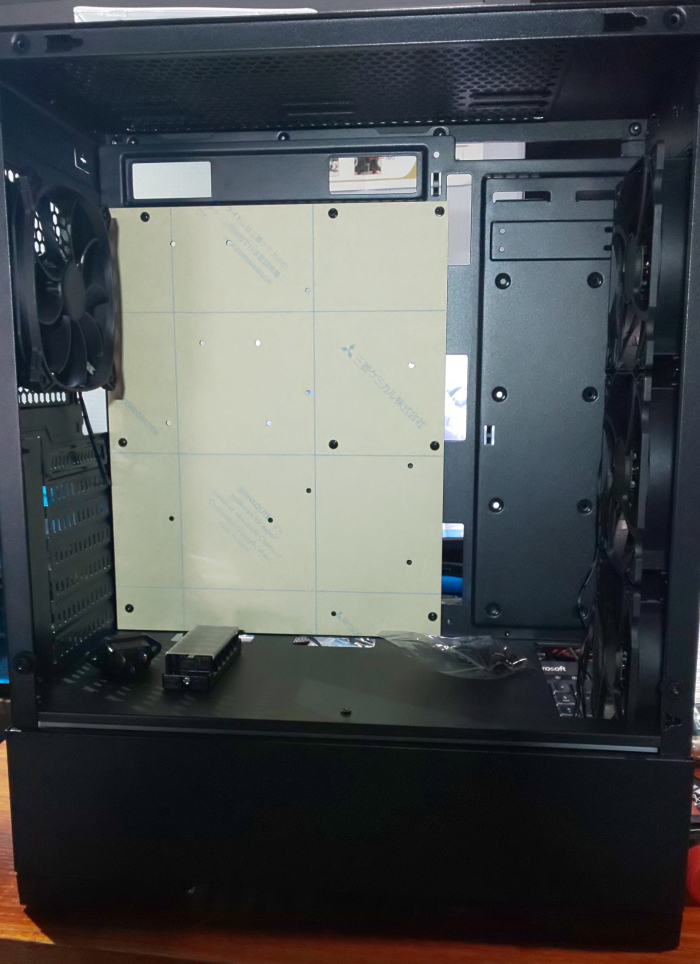 |
M-ATXケースはANTECです。
内部の作りもしっかりとしており、このケースを選んで正解でした。
ケースの価格も5500円ほどで、中途半端な電子部品用ケースを買うよりも遥かに格安で、しかも冷却ファンも簡単に取り付けられるため大変便利です。
カットしたアクリル板を仮に固定してみてネジの位置などを確かめておきます。勿論、取り付けはバッチリです。
マザー板がレーザーカット出来たので、ここからはマザーを仕上げて行きましょう。
あらかじめ計測しておいた各部品の穴位置もレーザーで穴が開いているので、わざわざドリルを使う事も無く簡単に部品を取り付けできます。 |
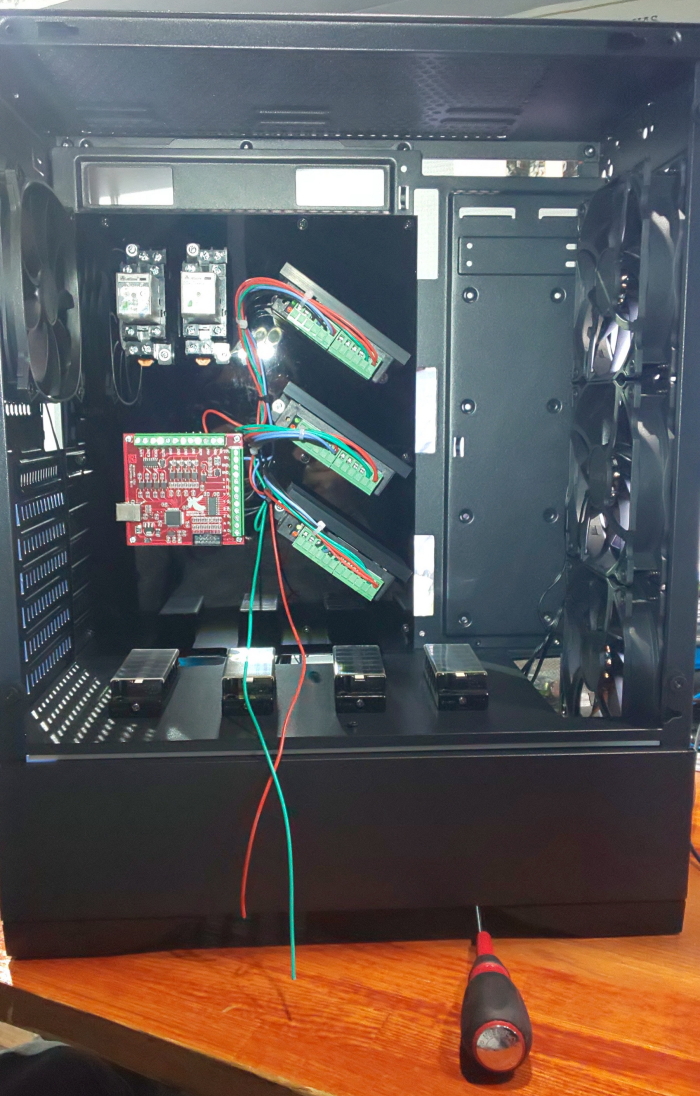 |
そしてこれが半完成のマザーボードです。
モータードライバーの冷却を考えて、3つのドライバーを30度の角度に傾けることで、右側の3つの冷却ファンの風がヒートシンクにしっかりと吹き付けられるようにしました。
少し離れてみて、冷却ファンの流れは問題ないか確認してみます。
なかなか良いのでは?と、少し自画自賛・・・。
まだ届いていない部品も有るのでもう少し作業が必要ですが、頭でイメージしたデザインに仕上がって行きそうです。
|
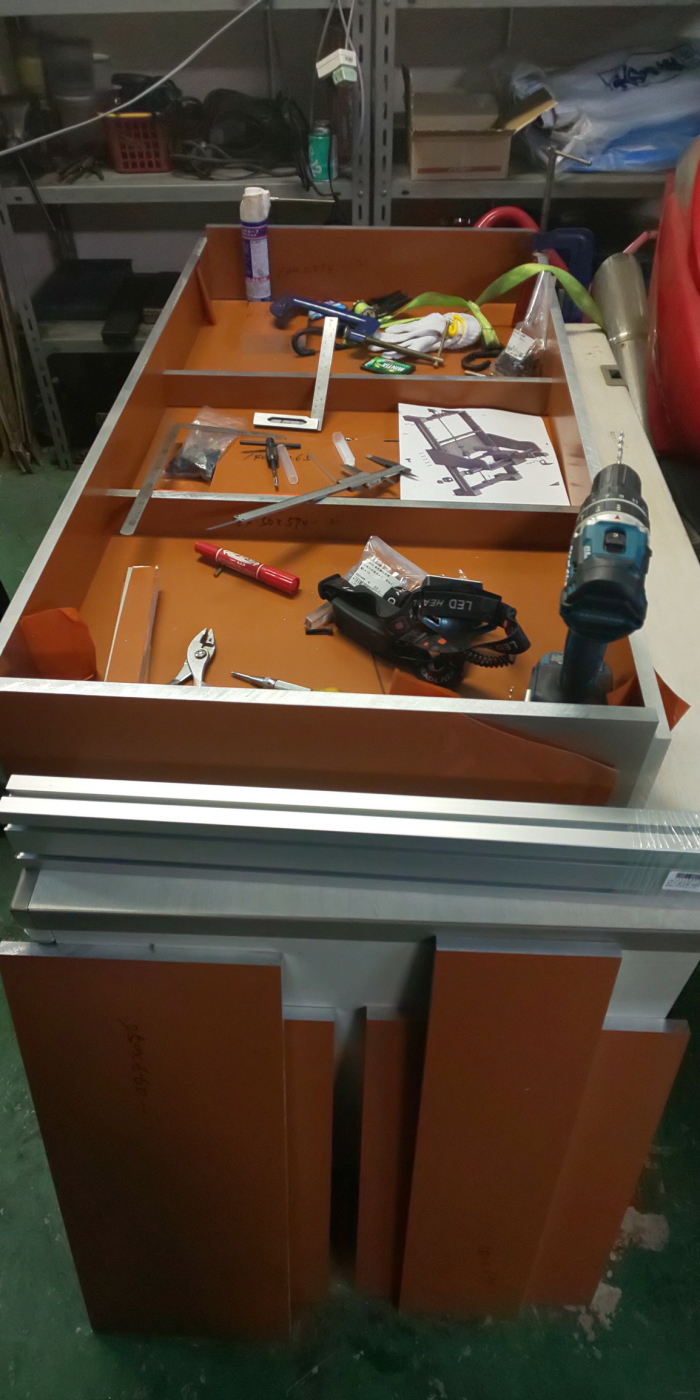 |
注文していたジュラルミン材料が届いた。AL2017の t=15mm
オレンジ色の保護シールが貼られている。
早速、各部の穴あけ加工に取り掛かります。
メインフレームの目の字構造が良く判るアングル。
穴あけ加工で苦労するのは、帯材の端面への穴あけ。
ボール盤の懐に入らないため、手工具で軸ズレが無い様に注意しながらひたすら穴掘りを行うのがつらい。
発注した材料の寸法が微妙に大きくカットされている為、それの寸法直しを小型のフライスで行うが、それもまた懐が足りなくて苦痛の連続だった。
そのような無理な作業が災いして、一部の穴あけにもズレが生じてしまい、その部分の補いを修正するのにもまた一苦労する。
それでもなんとか目の字フレームが完成した。
写真は仮配置の時の物で、ここからけがいて穴あけに入る時の物。
目の字フレームが完成したら、次は天板を固定する為にこの状態からひっくり返して表面への作業となる。(今は裏側)
もしかしたら、Y軸のボールスクリュー関係の穴あけを先に行うかも? |
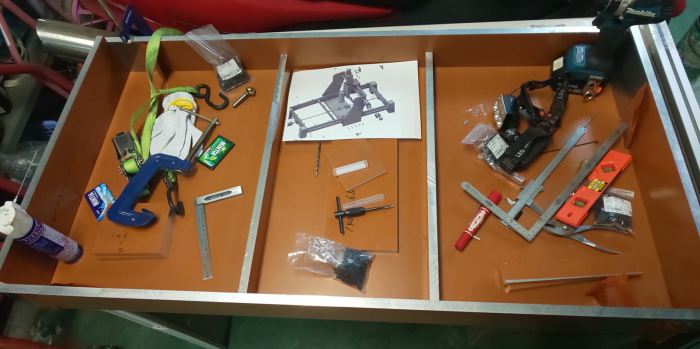 |
そこそこデカイので取り回しが大変。
組み立ての段取りも全て考えなければならず、手戻りも多くて大変では有るが大好きな作業なので夢中になれる。
作業中はそれこそ雑念が消えて加工や組み立てに没頭してしまう。
|
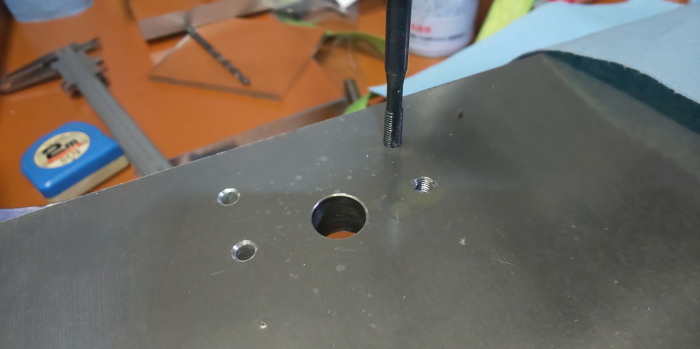 |
穴あけとタップでネジを立てる作業の繰り返し。
写真の穴はY軸のボールスクリューが固定されるベアリングブロックの為の物。
各部の締結は全てボルトを使用するため、ネジ立てが延々と続く。 |
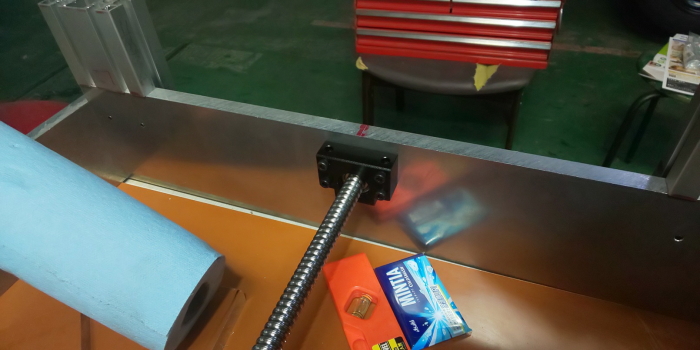 |
そしてベアリングブロックが付いた。
工程がひとつ進むと形になるので、心の栄養になる。 |
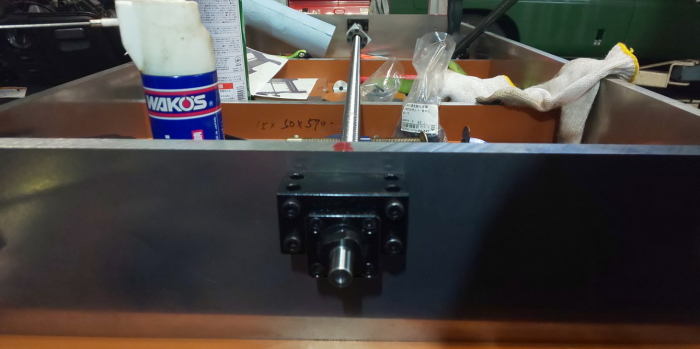 |
Y軸のステッピングモーターがここに取り付きます。
軸を通すのも一苦労が有りますが、こうやって形になると苦労が報われます。
形が出来ると暫くそれを眺めて、次の段取りなどに思考をめぐらせながらボーっとしてしまいます。 |
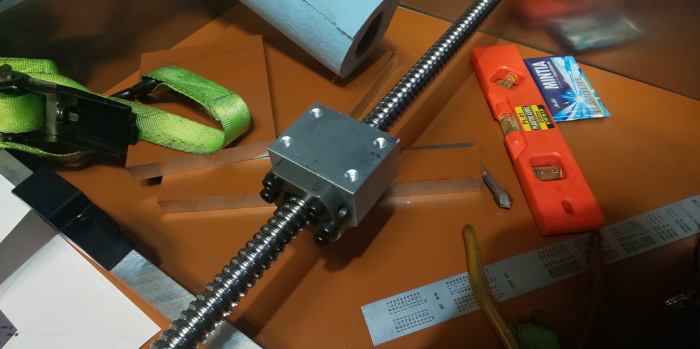 |
ボールネジにはこのようなブロックが嵌められており、シャフトの回転でこのブロックが移動します。ブロックは直接ガントリーを動かす部分なので、このモデルでは一番力の掛かる部分です。
その為シャフトは16mmの物を使用しています。 |
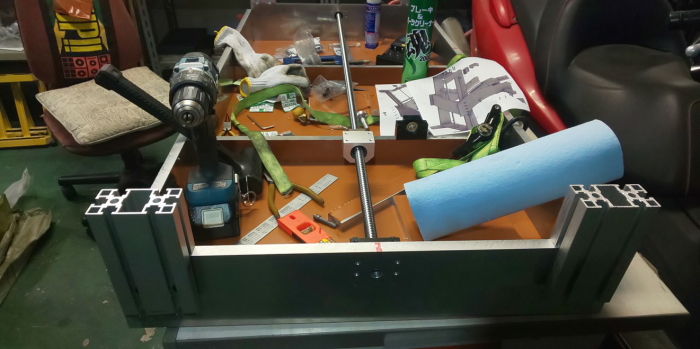 |
本体に足が付きました。
この足の穴部分にアジャスターを取り付けて、本体天板の水平を出します。
重量が掛かる部分なので40x80mmのアルミフレームを加工して使用しています。
将来的にはこのアルミフレームの溝を利用して、防音ケース(エンクロージャーと呼びます)を取り付けます。
本体フレームに足が付いたので、次の工程は天板の取り付けです。 |
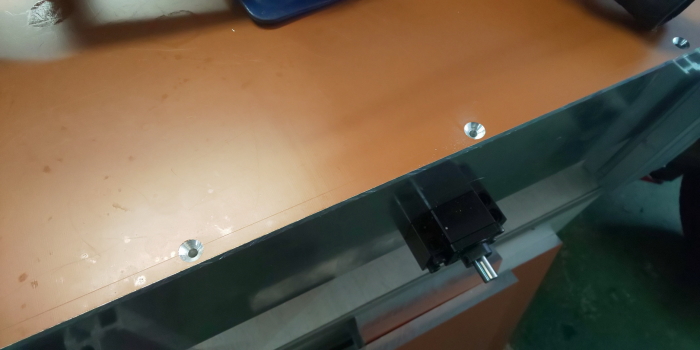 |
本体表面に天板を乗せて位置決めし、皿ビスで固定します。
皿ビスの埋まる皿加工も全て電ドラの手作業で行うので、刃先の暴れに注意を払いながら作業するのが疲れる。 |
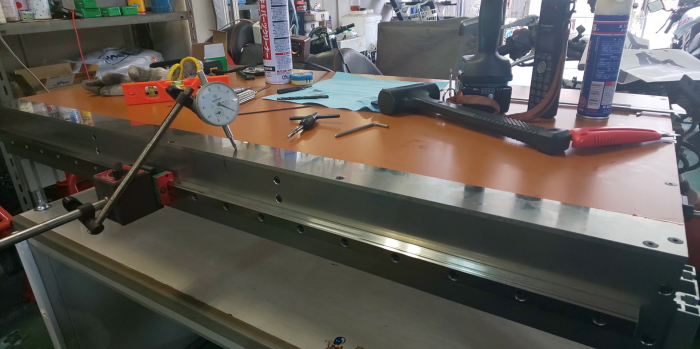 |
天板の固定が出来たら、次の工程はY軸のリニアレールの取り付けです。
ここからはCNC加工機の工作精度に直接響いてくる項目なので、部品の固定もダイアルゲージを使用して慎重に測定しながらリニアレールの固定ボルトを1本ずつ締めていきます。
ダイアルゲージはマグネットでベアリングブロックに固定していて、ブロックを前後にスライドさせると僅かなレールのズレが良く判ります。
1本のレールの調整だけではなく、反対側のレールとの高さ調整も見ながらなので、もの凄く時間がかかる作業ですが疎かには出来ません。 |
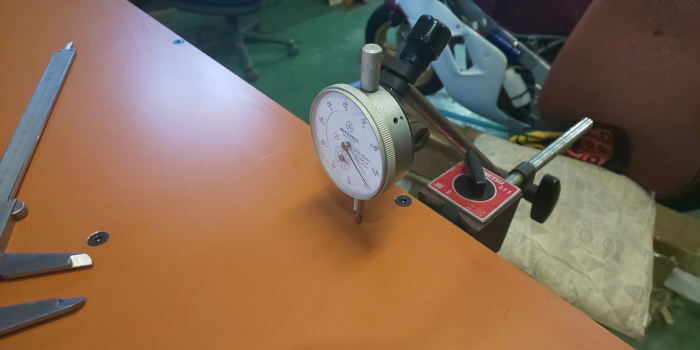 |
天板の各所にゲージを当てて、極力各軸の直交が得られるように仕上げていきます。 |
 |
Y軸の次はX軸の製作です。これも同じく2本のレールを限りなく平行に組みつけていきます。
因みに使用しているリニアレールは高精度のように思いますが、良く曲がっていてそのまま固定したら稼動後にはとんでもない加工物が出来上がります。
焼きの入った製品でネジ穴が多く空いているので、直線は面白いほど狂っています。
それらの狂いもゲージを当ててしっかりと組めば綺麗な直線になるので、組方さえ知識が有れば、このような製品でも十分に費用対効果が得られるわけです。
|
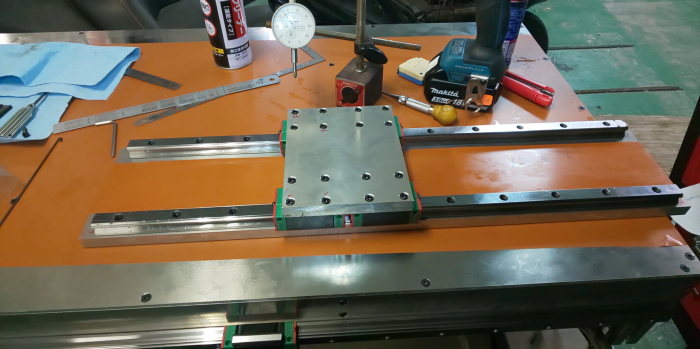 |
完成?したX軸単体。まだ本当の完成ではないのですが、取りあえず形にはなりました。
この真ん中のプレートにZ軸の機構が取り付けられます。
そしてそこのモーターが取り付けられるので、もの凄い重量を支える部分です。しかもそこから加工のストレスが掛かると言う・・・。
|
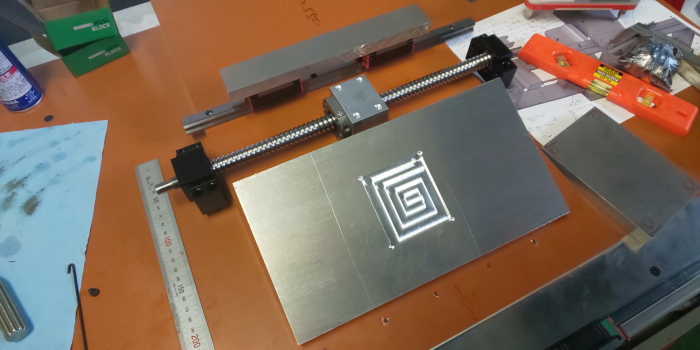 |
このプレートはZ軸のスピンドルモーターを取り付ける部分です。
スピンドルを上下させる為のボールスクリューブロックがはまる部分を小型フライスで手作業で切削加工しました。
CNC加工機が完成したら、このような加工も楽チンなのですが・・・。 |
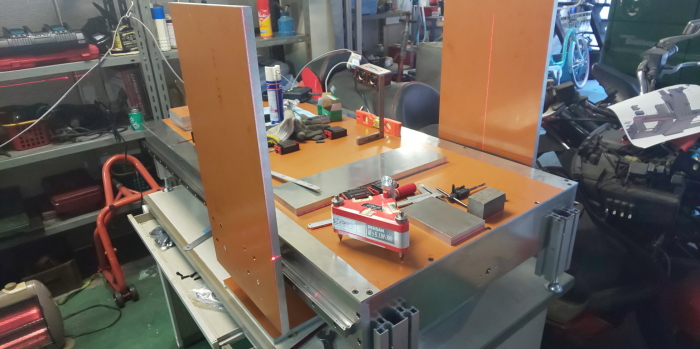 |
X軸を支えるガントリーの両脚を立てています。レーザーを使用して角度の狂いが出ないように監視しながら作業を進めています。
17S板の単体重量が意外に重いのですが、ガントリーを支えるスライドブロックは全く抵抗が無いような滑りを見せています。 |
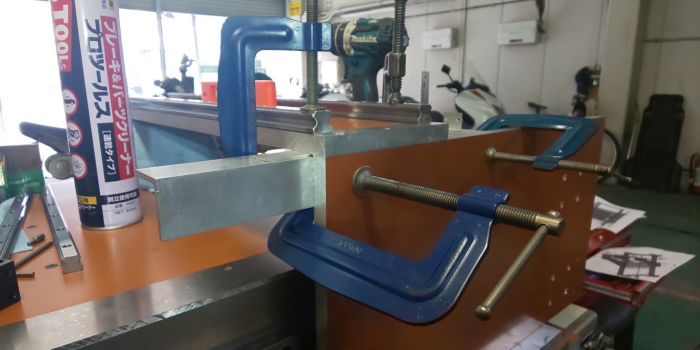 |
ガントリーの脚に対して、X軸のブレースを固定するボルト穴を開けるためにジグを組みました。
材料が大きくて重い為に加工時の取り回しに苦労しますが、正確な穴あけを行えるようにジグを組むと多少は楽が出来ます。 |
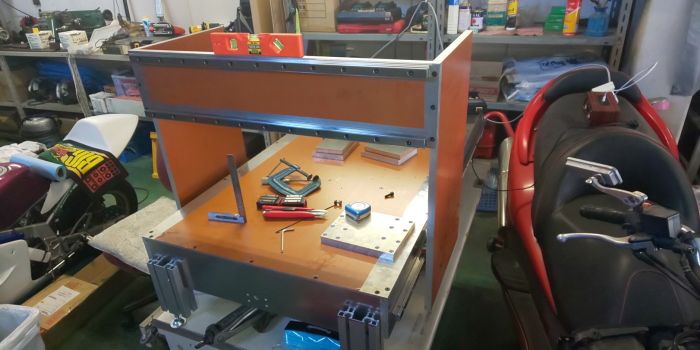 |
そして取り付けられたガントリー・・・。レベルもバッチリと出ています。各種作業でここからまた取り外しますが。
取りあえずは加工精度の確認でレベルだしをしてしまうと言う・・。
形になったガントリーを手で押すと、ずっしりとした重量は感じますが軽くスライドします。 |
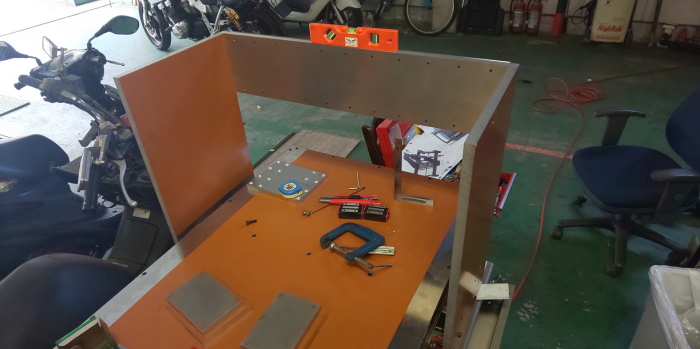 |
ここからはZ軸への検討に入ります。作業の手順などを事前に検討して、各部を加工していかないと途中で手戻りが発生して効率が落ちます。
といいつつ、しょっちゅう手戻りしていますが。 |
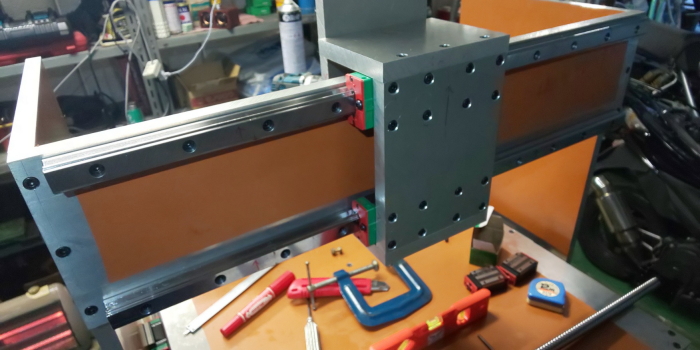 |
ガントリーにZ軸のバックプレートを取り付けています。
海外の自作CNCマシンで良く見るX軸のレール配置とは全く逆の方式で、裏側にレールを組んでいます。
理由は作業が進むと判るのですが、このレールを前側に配置するとスピンドル周りの取り付け位置が大きく前方にせり出します。
すると、スピンドルなどの装置重量が半端無く重いためにY軸のベアリングブロックに大きな偏向重量が掛かるなどの、負荷のアンバランスが生じるのではないかと考え、このような配置で設計しました。
実際の効果の程は検証できないのですが、自分の気休めみたいな物です。 |
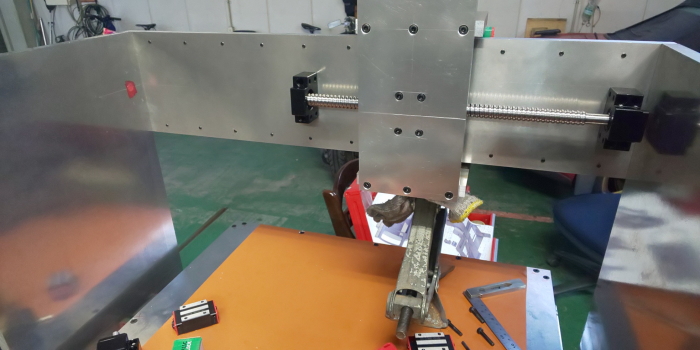 |
取り付けたZ軸プレートを使用してX軸を左右に動かす方式です。
X軸を構築するのに、Z軸のパーツに手を付けていたのはこのためです。
X軸のスクリューシャフトを固定するベアリングブロックの取り付けの検討中です。
部品注文の際に指定した物とは違うブロックが来ている為に、取り付け方法や各部の取り回しなどがやりにくくて面倒くさい状態です。
正規の部品を待つには時間が無い為、苦労しながらも無理やり形にしています。
寸法の短いZ軸のシャフトを使い、X軸のブロックの固定位置を割り出しています。 |
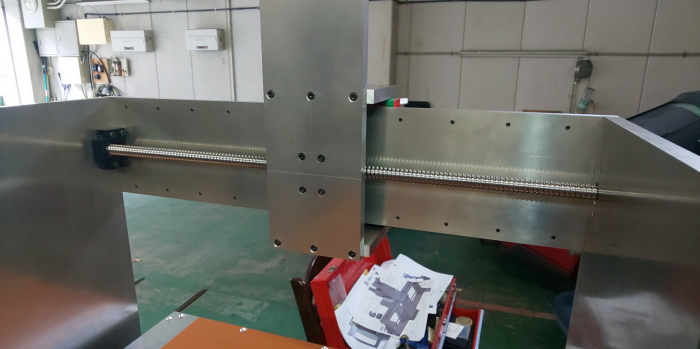 |
そして取り付いたX軸のスクリューシャフト。
注文した部品と違う物が届いた為、取り付け方法他、色々と不細工ですがひとまず良しとします。 |
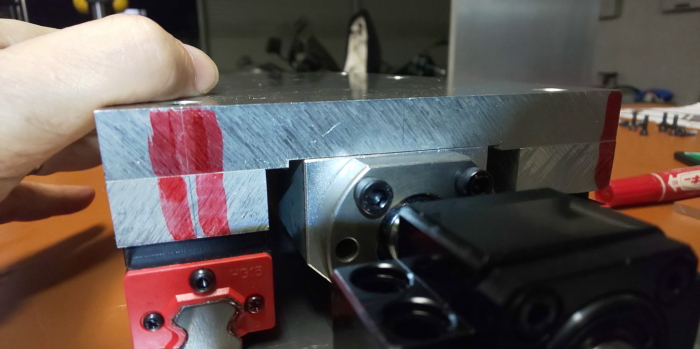 |
これはZ軸のスピンドルマウントへの加工の結果です。
ベアリングブロックとマウントプレートとの間に下駄を履かせたのですが、それでも高さが合わず、フライスで手作業で高さ合わせを行いました。
|
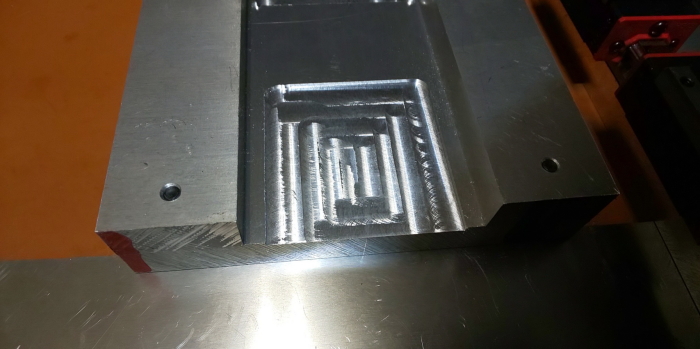 |
高さ合わせで切削したプレートを裏側から見たもの。 |
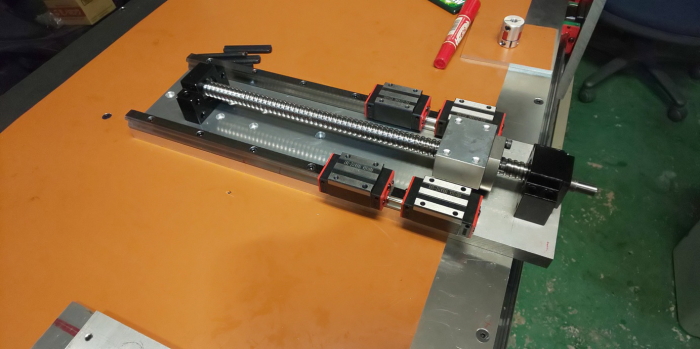 |
色々な作業をこなしながら少しずつですが完成へと進んでいます。
写真はZ軸の各部品の穴あけ検討中のもの。
ボール盤で穴あけを行いますが、必ずずれるのでそのズレを吸収できる作業の工程検討が重要です。 |
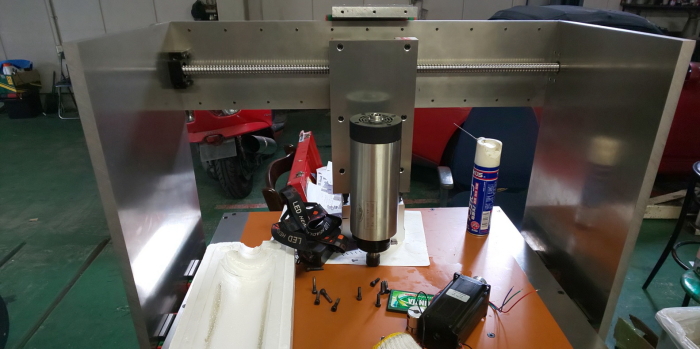 |
仮にスピンドルを合わせて見て、工程に問題が無いかを注意深く考えます。 |
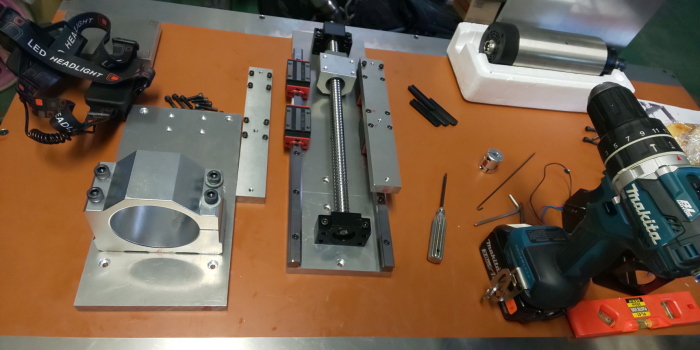 |
細かな穴あけ作業を継続しつつ、各部の組み立てを進めていきます。
左側のプレートには、スピンドルマウントが取り付けられています。 |
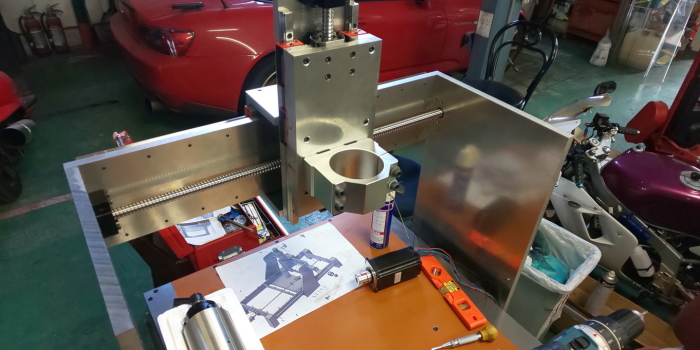 |
組み立てた状態のZ軸。
やっとCNCマシンらしい姿になりました。 |
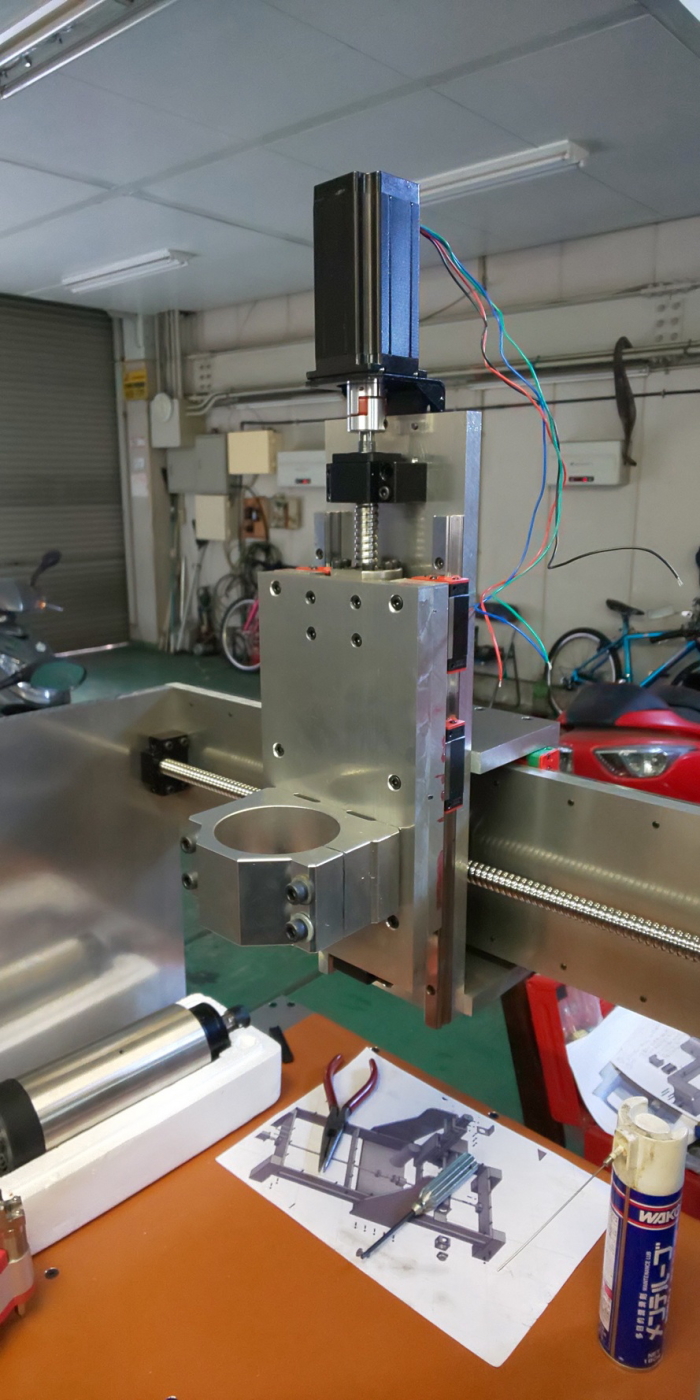 |
そしてZ軸のステッピングモーターの取り付け完了。
全体的に細かな位置調整が行えるように考えて作り込んでいます。
このように背が高くなるとなかなかの見栄えがします。
Z軸はコントローラに接続すれば動く状態です。
これからリミットSWなどの取り付けが必要ですが、この姿になると気持ちも上がります。 |
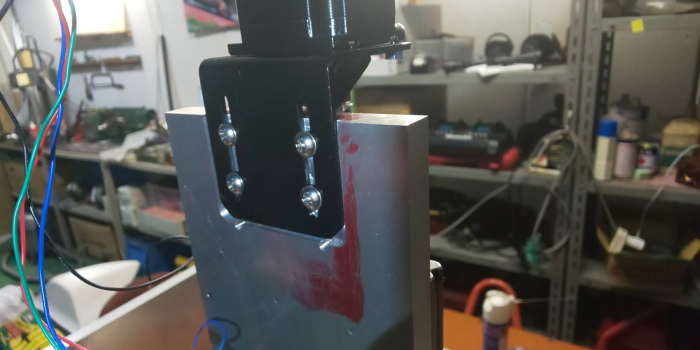 |
ステッピングモーター取り付けの裏側の様子。
位置調整が可能なスライド構造にしています。 |
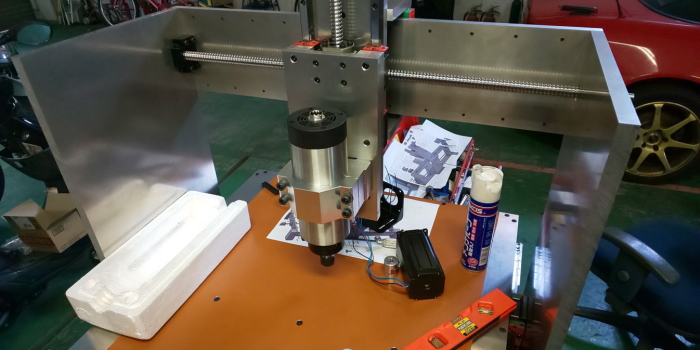 |
とうとうスピンドルが取り付きました。
CNCマシンの姿です。
しばらく見とれてしまいました。
苦労が報われる瞬間でも有ります。 |
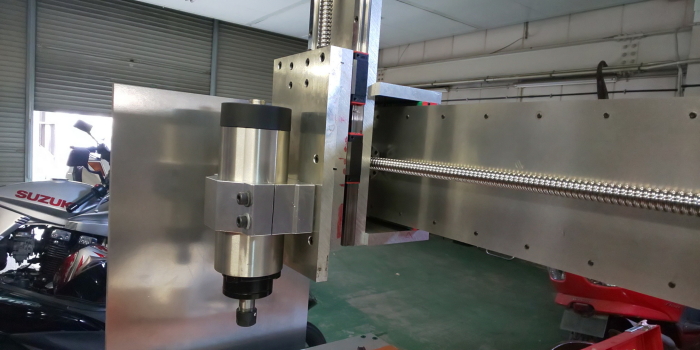 |
X軸の端まで動かすとこんな感じ。 |
 |
レーザーで位置の割り出しを行い、左右のストロークを測定中です。 |
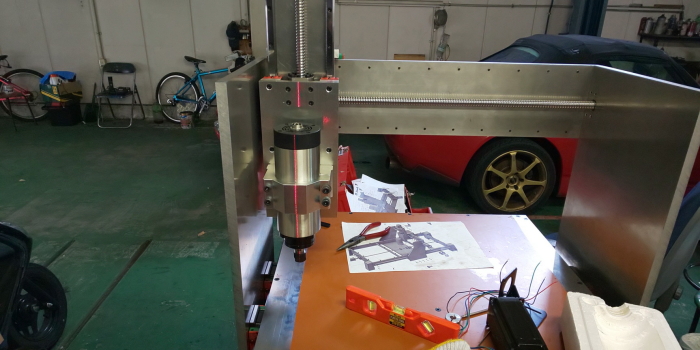 |
左右のストロークは丁度500mmで設計通りでした。
|
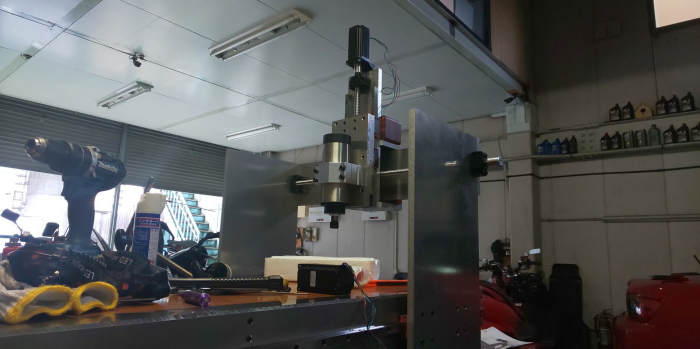 |
次はX軸のステッピングモーターの取り付けです。
この作業も間違い部品のベアリングブロックに邪魔をされていて、モータ取り付けがややこしいです。 |
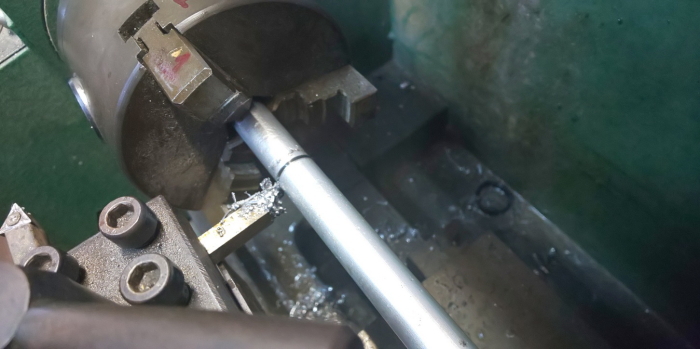 |
まずは旋盤でアルミ棒を削り出して・・・・。
両端部に穴あけ、M5ネジ立て。
これを合計8本分! |
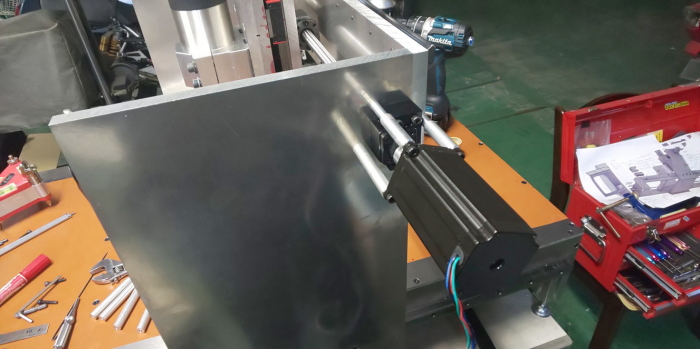 |
そしてステッピングモーターが取り付きました。
黒いブロックが邪魔でモータを傾けざるを得ず、しかもモーターの足は3本しか取り付かなくて・・・。
でもガッチリと固定できているのでひとまず良しとして、先でCNCで切削部品を作り置き換えることにします。
これでX軸も完成!
後はY軸です。 |
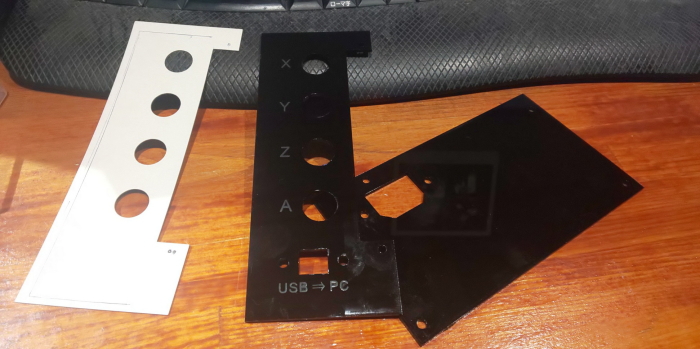 |
以前作っていた試作型紙を基に製品をレーザー加工機で切り出しました。
各軸が判りやすいように文字も彫り込んでいます。 |
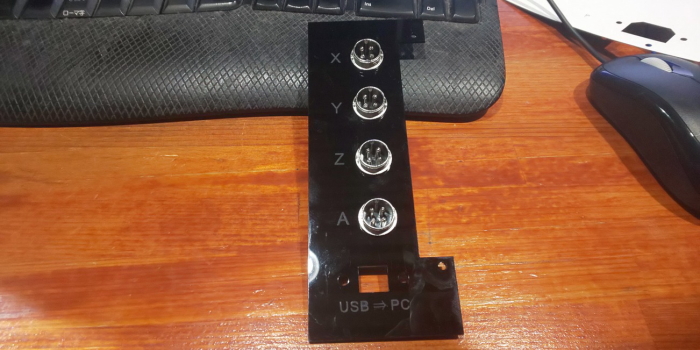 |
プレートにコネクターを組み込んで行き・・・。 |
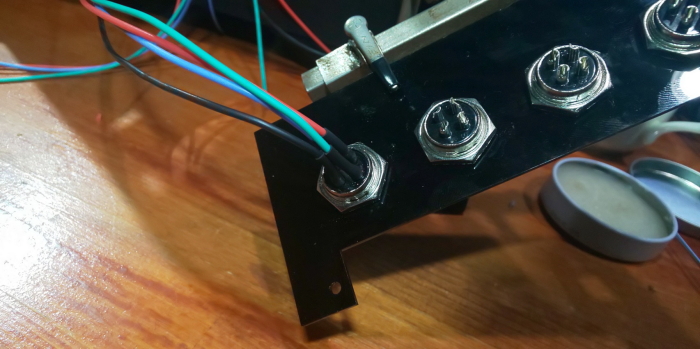 |
各軸への配線を色分けしながら仕上げていきます。 |
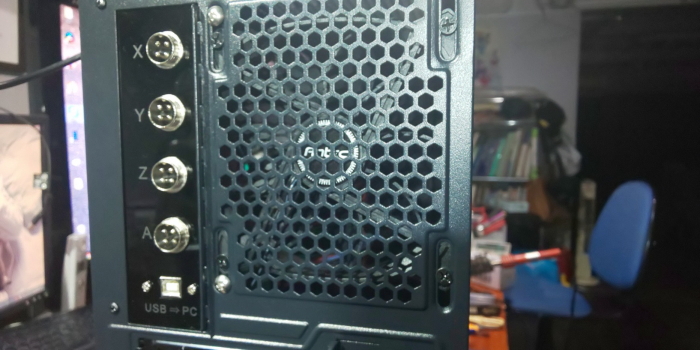 |
そして、USBソケットも組み込んで完成したソケット周りです。 |
 |
初めての電源投入!。ドキドキする瞬間です。
無事に動いてくれと願いつつ、リモコンを操作するとあっけなく動きました。
まだMach3の細かな調整が必要なのですが、取りあえずは動いた!
しばしの間、感動に浸ります。何年もかけて温めて来たCNC加工機を導入する夢が現実になった瞬間です。
|
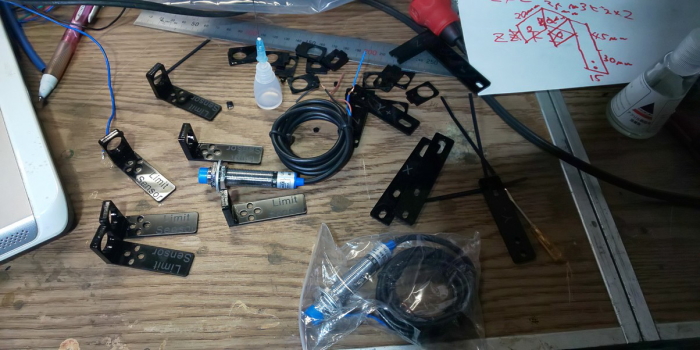 |
機械が動くと、動作範囲の領域を超えると当然トラブルになります。
そこで動作範囲を規定する為に、各軸のエンドポイントをセンサーで検出してマザーボードに知らせる必要があります。
作っているのはセンサーをCNCへ固定する為のマウントです。
各部を実測して、CADで仕上げてレーザーカットして・・・・。
後は接着剤が硬化したら組み込みです。 |
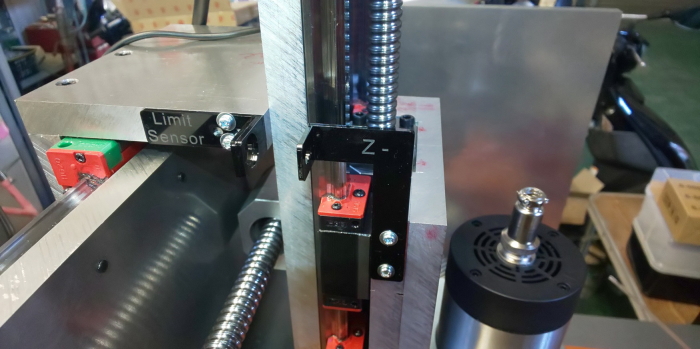 |
このような感じで取り付けます。
これは主軸の上下を範囲規定するZセンサーの位置です。 |
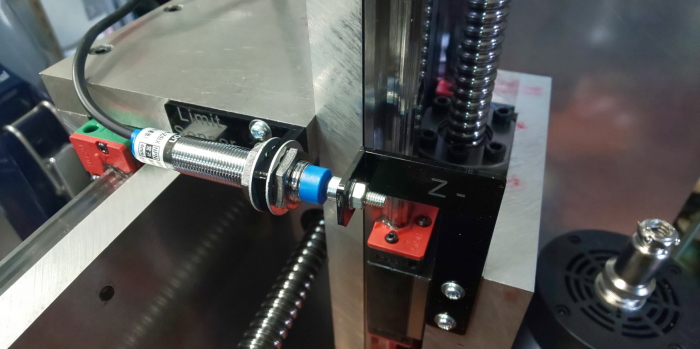 |
センサーを取り付けて、対向する動作部分にはセンサーが反応するように金属を固定しています。要はボルトの頭をセンシングさせる訳です。
センサープレートは各部位が調整できるようにしてあるので、若干の停止位置調整が可能です。
実際にCNC機を動かしながら細かく調整していきます。
このセンサーの検出位置で加工できる範囲が決まるので、なるべく広く取れるように考えます。 |
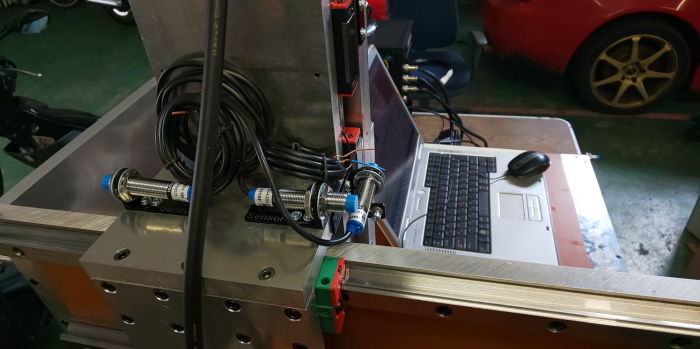 |
Z軸の裏側にはX軸のリミットセンサーが左右に並びます。
なぜこうしたかと言うと、センサー本体を機械の端に固定すると、センサー本体のお尻が意外にはみ出すのです。
はみ出したセンサーに体なりが当たる可能性があるので、なるべくはみ出さないように考えた結果このような配置となりました。 |
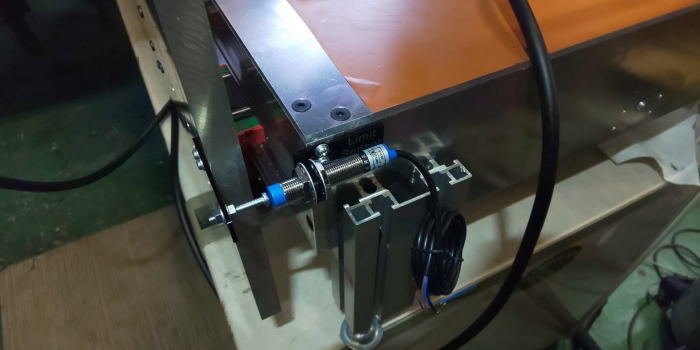 |
こちらはY軸のリミットセンサーです。
ガントリーに取り付けたプレートにボルトが取り付けてあり、このボルトがセンサーの検知範囲に来るとリミット判定で停止します。
|
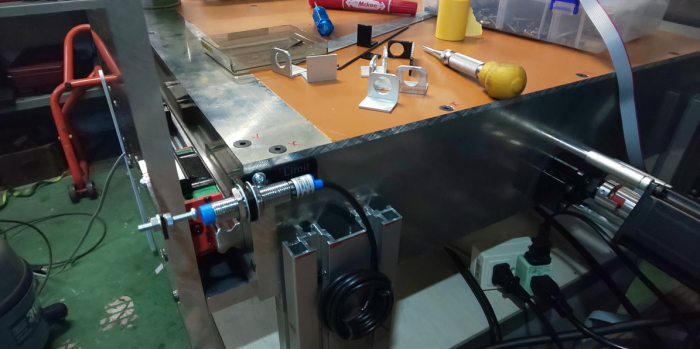 |
Y軸の反対側にも。
盤上にあるアルミのプレートは、当初センサーを固定する為に作った物ですが、仕上がりが気に入らずに使用しませんでした。
このような余分な作業が多く含まれていますが、結果的に仕上がりがかりっとした物になるので、やり直して正解です。
|
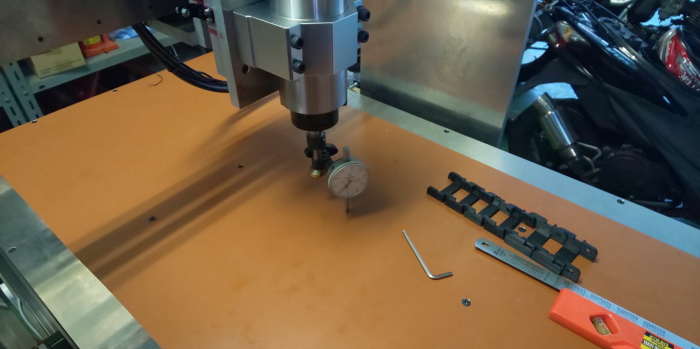 |
リミットセンサーが稼動したので基本的にはCNC加工機として完成です。
主軸への配線も完了し、現在は各部のアライメントの測定と調整です。
写真の作業はスピンドル軸に取り付けたゲージで、先端工具の傾きが出ないように主軸位置を調整している状態です。
もうデータを送れば切削作業が可能です!。
2020/02/04 |
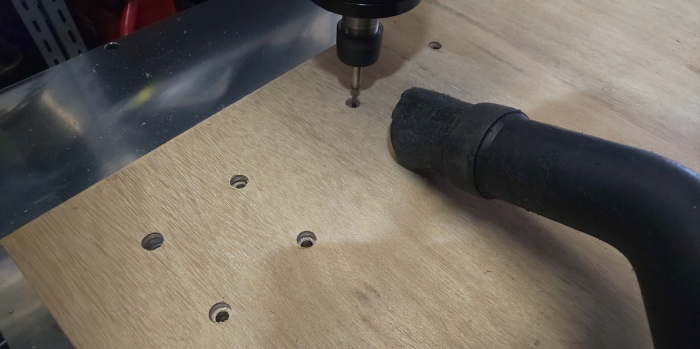 |
CNC加工機による初作業です。
何を切削しているかと言うと、CNC加工機の作業ベッドを製作しています。
これは様々な考え方のひとつで、このCNC加工機は切削材料はほぼ、ジュラルミンです。
ジュラルミンの切削で切り込み量も少ないので、切削時に殆ど冷却&潤滑クーラントを使用しません。
いわゆるドライ切削なので、作業ベッドを合板仕様にしています。
メリットは、ベッドが傷めばすぐに安価で交換できる。ワーク固定が枠にとらわれないなどが有ります。
デメリットは超高精度の切削には向かない事ですが、現状での作業要求が超高精度ではないので、このような形態をとっています。
|
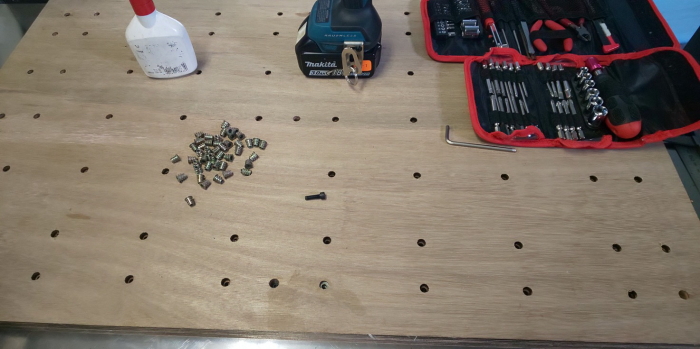 |
作業ベッドに開けている穴は、写真のような埋め込みナットを埋設する為です。
このネジ穴を使用して作業ワーク(切削物)を固定します。
なので少し深く掘り込んで埋めています。
CNCで穴あけ加工すると、図面の通りに加工できるのでもう手放せません!。 |
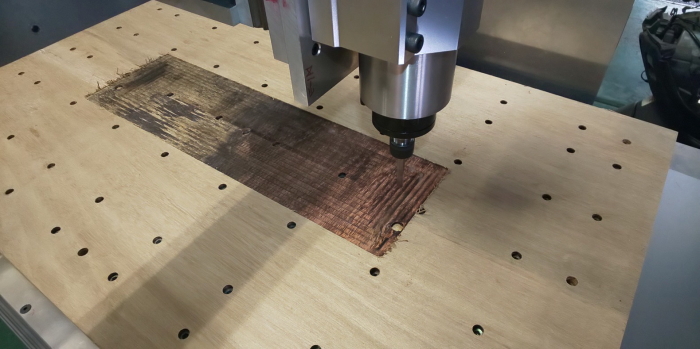 |
そしていきなりの作業ベッドへの切り込みです。
これはCNC加工機に設置した作業ベッドの平面を出す作業です。
市販の合板の厚みなど極めて不正確なので、機械にきちっと取り付けた後でその表面を平らに切削するのです。
本来広い面積を切削する際には、フェイスミルと言う広く削れるエンドミルを使うのですが、今はまだ持っていないので時間の掛かる通常のエンドミルで作業しています。
写真の右側の厚みが相対的に左よりも分厚くて、エンドミルが右に行くに従い沈んでいくのが見ていて少し不安になります。
CNC加工機自体のベッドはダイアルゲージで測定して平面をきちっと出しているので、潜り込んでいくエンドミルは平面を出しに行く為なのだと思いながら見ています。 |
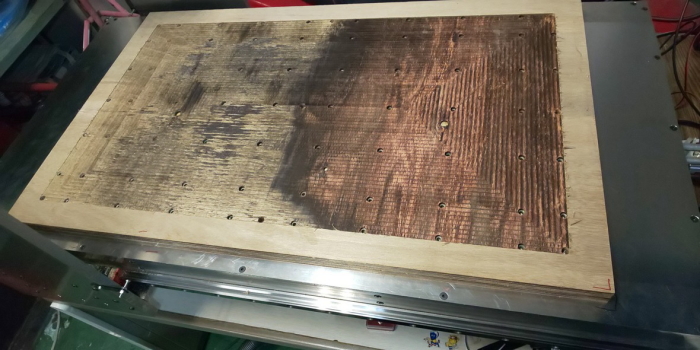 |
一旦全て面出しが完了した状態です。
右側が分厚い為に左側の切り込み量が少なく、見た目のバランスも悪いのでもう少し削り込んでみます。 |
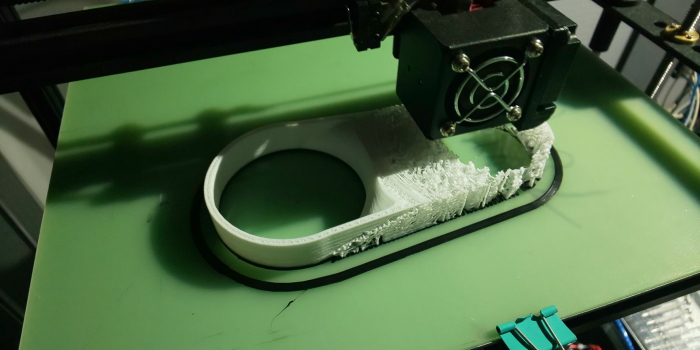 |
3DプリンターでCNC加工機の部品を製作しています。
何かと言うと、エンドミルが材料を切削するととんでもない量の切りくずが噴出します。
そのままだと機械の周辺があっという間に切りくずだらけになり、とてもでは無い状態となります。
そこでこのような物を製作して・・・
写真の右側のごちゃごちゃした物はサポート材です。何も無い空間に部品を定着させる為の足がかりのような物です。 |
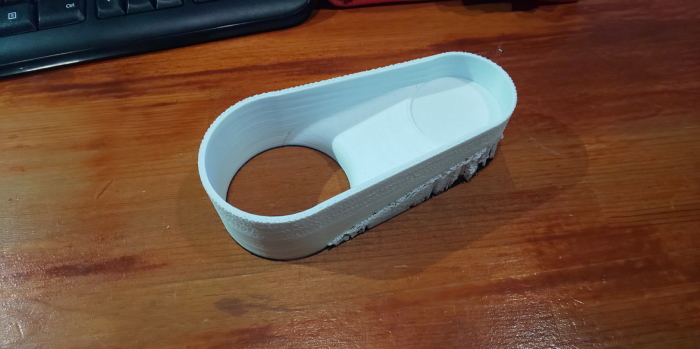 |
そして出来た物がこれです。左の穴がエンドミルの部分を覆うように囲みます。 |
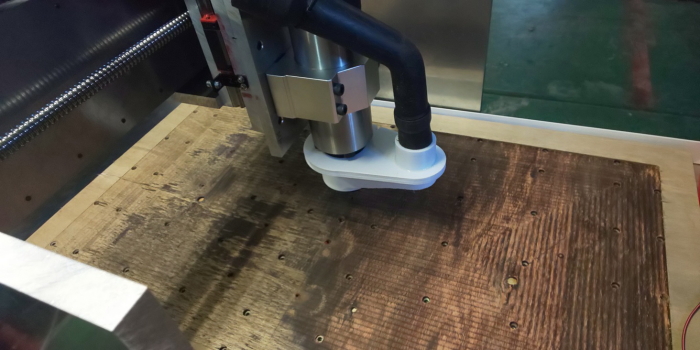 |
他の部品と組み合わせて取り付けた状態のプロトタイプ1型。
この状態から切削させてみて、ゴミの吸引状態から今後の変更を検討します。
今の所85点くらいのスコアです。それでも無い事に比べると雲泥の差です。 |
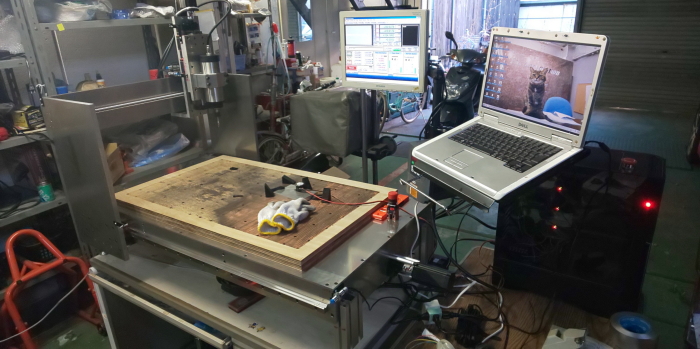 |
取りあえずの現状の姿を載せておきます。
一応、ここまででこの記事は終了とします。
2020/02/14
CNC加工機自体はこれからもバージョンアップしていくので、その時には加筆します
何かの参考になれば。 |
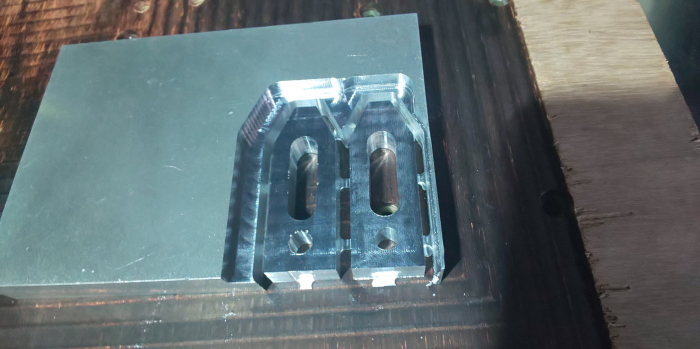 |
CNC加工機で切削した部品を少し紹介します。
写真はワークを固定する為のクランプです。
7075ジュラから切り出しました。
CNCの専門家の方が見れば大したことは無いのでしょうが、今までこのような作業が自社内では不可能だったことを考えると、こちらとしては十分な成果といえます。
|
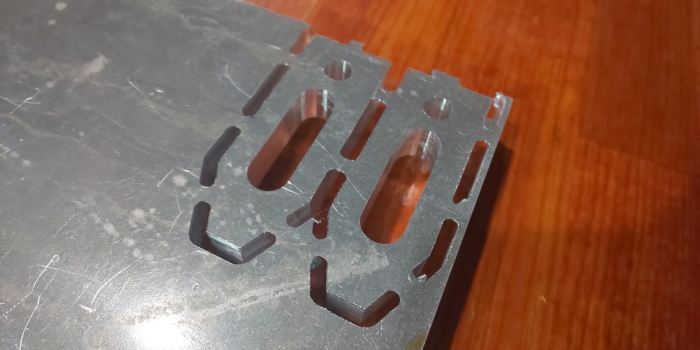 |
同じ物を裏から見たもの。
部品が脱落しないようにタブと呼ばれる枝を残して仕上げています。
これは部品の切削最終段階になると、エンドミルの切削圧力で部品が動いてしまいワークから脱落し、作業が失敗するのを防ぐ為の物です。
この状態からはニッパーで切り出して端面を仕上げれば完成です。 |
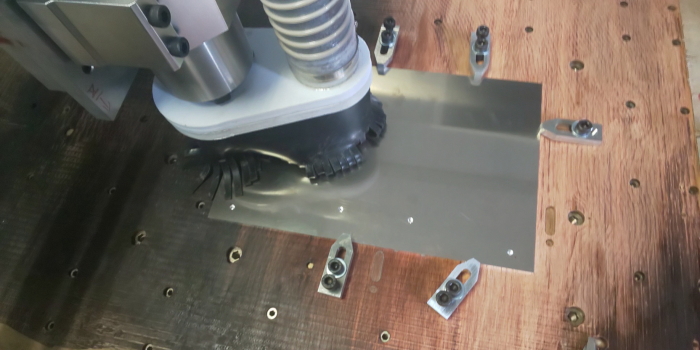 |
ワークを押さえるクランプはこのような感じで使用しています。
ワークは3tの17Sに穴あけ加工中です。
バキュームシューの性能は抜群で、アルミ板の切削であればほぼ100%クズは出ません。
切削中に試しにバキュームを停止してみると、凄まじい切りくずが撒き散らされていて効果の程を感じました。
エンドミルは2mmのHSSを使用しています。
ドライ切削の為、送り量と切り込み量は共に0.2mmで行い、エンドミルの消耗を防いでいます。
その為作業時間がかかりますが、高精度の位置切削が出来るので気になりません。 |
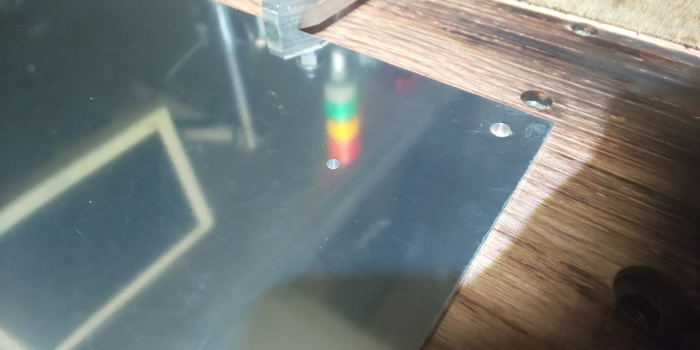 |
見難いですが仕上がりはこんな感じです。
綺麗に穴が開けられていて気持ちの良い物です。
ここからタップでネジ加工を行い、組み立てに入ります。
|
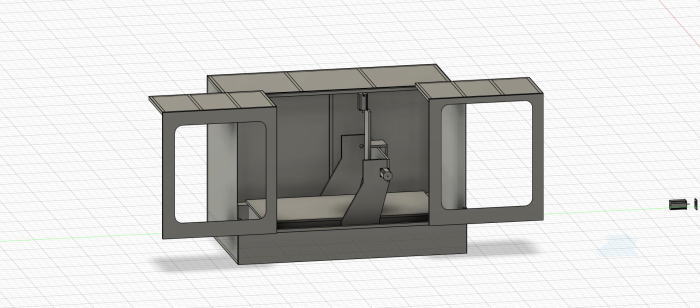 |
CNC加工機で切削作業を行っていると、加工機の運転時間が長時間に及ぶことが度々あります。
すると問題となるのが加工時の音ですが、送りを少なく、切込みも薄くすることで多少音は抑えられますがその分、加工時間が伸びます。
当初から想定していましたが、なるべく早く防音設備を構築したいと考えています。
カバーの形状は概ねこのようなデザインで仕上げていこうかと。
しかし、その前にいくつかの機能をCNC加工機に持たせておきたいと考えています。
まずは、Mach3からスピンドルをコントロールする仕様に変更します。 |
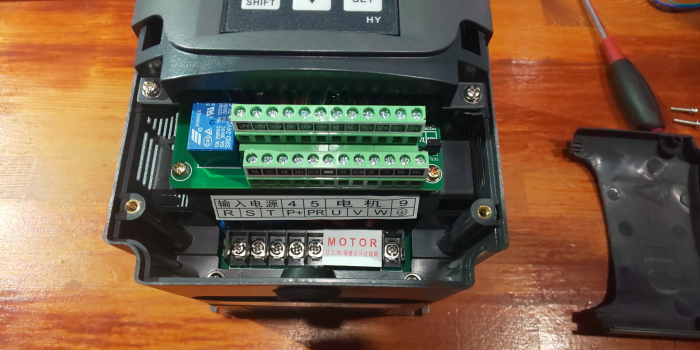 |
Mach3からスピンドルをコントロールするには幾つかの方法がありますが、私が選んだ方法はPCからRS485経由でVFDを制御する方法です。
この方法は構成がシンプルで、複雑なリレー構成や配線が必要無く、簡単に構築できます。
この情報は海外のサイトで紹介されていたもので、この方法を日本でやっている人がいるのかどうかは検索していないので判りません。
写真は現在使用しているHY VFDですが、制御信号ターミナルが二段に分かれています。そのターミナルの下の段、写真で言う手前側の右端の2つのターミナルがRS485信号を受ける接点です。
この2つのターミナルに次に示すUSB-RS485ユニットからの配線を接続します。VFDにはRS+とRS-の表示がありますので極性を合わせて接続します。 |
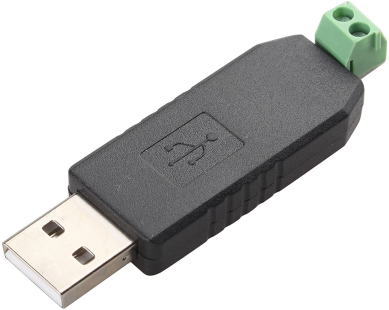 |
左写真の物がUSB-RS485ユニットです。Amazonで購入
この端の緑色のターミナルに2線を接続し、VFDのRS端子へ接続します。
PCにはこのユニットを認識させるドライバーをあらかじめインストールしておきます。
ドライバーの情報は、購入時に閲覧したAmazonの評価欄でキーワードが出ていたので、それをもとに海外サイトでダウンロードしました。
ちなみに、この商品の価格は約500円程度でした。 |
ここからが少し手間なのですが、作業の流れを下に示します。
1 USB-RS485 ユニットのドライバーをインストールする。
2 PCのデバイスマネージャーで認識を確認し、COMポートの
番号を確認しておく。(後で必要)
3 VFDとUSB-RS485を2線で接続しておく。
4 海外サイトにてMach3 RS485 HY VFD 等のキーワードで、
Mach3内部で動作するVFD駆動プラグインを探してダウンロードする。
(ページ下部にリンクしています)
5 ダウンロードしたプラグインをサイトの指示に従い、Mach3の
ルートフォルダに有る、pluginフォルダー内にコピーする。
6 Mach3を起動し、Configプルダウンから,Plugin Controlを開き、該当する
プラグインが見えたら左側の黄色の部分をクリックする。
|
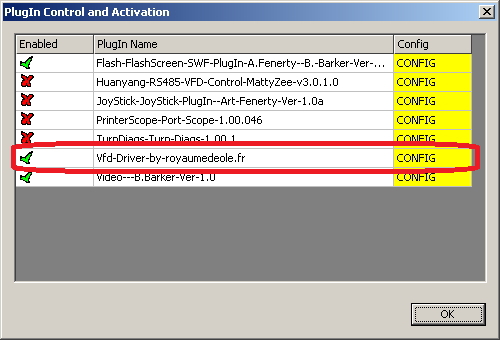 |
7 クリックすると右画面が出るので、先ほど確認したCOMポートの番号を入力。
その他の項目は触らないでOKで閉じる。 他にも窓が出る場合すべてOKで閉じる。
8 VFDのパラメーターでRS485を受け付けるように以下のコマンドを入力。
Parameter |
Value |
Description |
PD001 |
02 |
Enable commands on port rs485 |
PD002 |
02 |
Enable speed control on port rs485 |
|
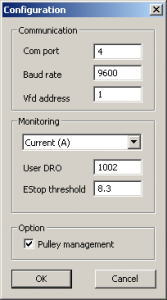 |
以上で間違いがなければMach3がVFDを認識します。一度Mach3を閉じてから
VFDの電源を先にONにして、Mach3を立ち上げるとVFDのコントロールが行える
ようになります。
スピンドルを回転させるにはMach3の右下画面のSpindleSpeedの欄に
10000 Enter で値を入力し、上のSpindle CWF5ボタンを押すと
スピンドルがスタートします。
G Codeでスピンドル回転数が定義されていれば、G−Codeを走らせた時点で
自動的にスピンドルが回転します。
切削が終了すればスピンドルが停止するように設定も可能です(GeneralConfig)
以上、少しややこしいですが、流れがわかれば極めてシンプルな方法でスピンドル
をコントロール出来るようになります。
2020/05/15追記 |
注意点としては、VFDの電源を先に立ち上げておかないとMach3が認識できず、立ち上げ時に質問をしてきますのでNOで立ち上げるか、先にVFDを立ち上げてからMach3を再起動しましょう。
NoでMach3を立ち上げるとVFDのコントロールはできません。方法はありますがここでは割愛します。ソフト再起動の方が速いためです
参考までに海外サイトのリンクを張っておきますが、いつまで閲覧できるか等判りません。
http://royaumedeole.fr/informatique/plugin-mach3-pour-vfdhuanyang/mach3-plugin-for-huanyang-vfd/
https://www.cncnutz.com/2017/05/mach3-and-uccnc-spindle-control-with.html
ファイルのダウンロード等自らの判断で行ってください。
悪意有る者がファイルをウイルスに置き換えている可能性も否定はできません。
海外の情報はご自分の責任の範囲でどうぞ。 |
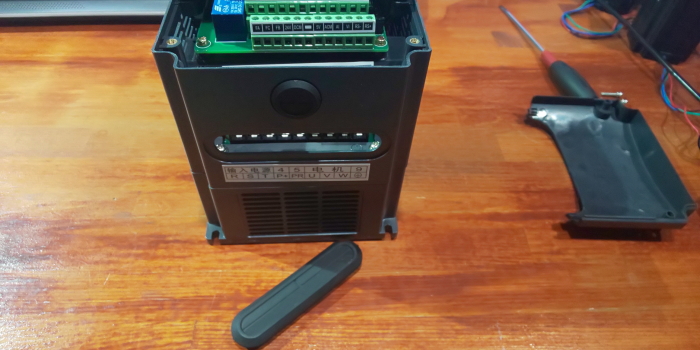 |
HY VFDを使用しているのだが、このVFDに搭載されている冷却ファンがとにかくやかましく、電源投入直後から延々と騒音をまき散らしている。
そこでその騒音を何とかすべしということで、情報を探していたら見つけたのがこれを利用して静かにしていただく方法。
|
|
温度が45℃になるとSWがONになる、いわゆるNOタイプの温度スイッチを使用する方法をYoutubeで見つけた。VFDの後部にあるやかましい冷却ファンの配線にこのセンサーを割り込ませて、センサー部分を熱源近くに設置することで、温度が低いときには無音で温度が上昇すれば冷却ファンが回転するというものに変身させた。
実際にVFDの電源を入れてみると無音・・・。
一瞬、本当に機能しているのかと疑ったが、PCから回転させるとちゃんと指定回転数で回転するので大正解。これで図面を見ながら考えている時に騒音で邪魔されないで済む。
Amazonで購入 2つセットで数百円でした。
なぜ初めからこのような仕様にしていないのか?と言う位、機能が進化した感じがする改造でした。
2020/05/15 追記 |
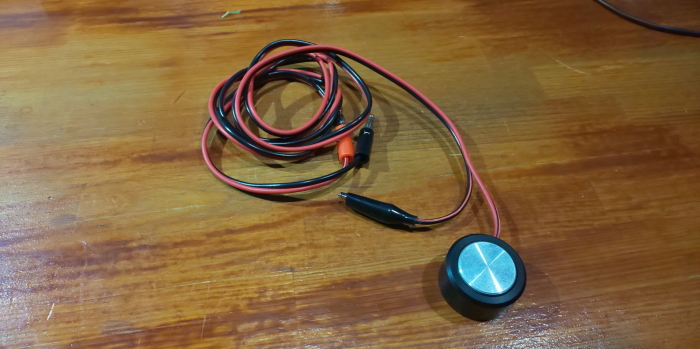 |
CNC加工機を使いだすと頻繁に行う作業がToolChange、いわゆるエンドミルの交換です。
切削内容に応じた刃先のエンドミルに交換するのですが、その都度必要なのが対象物とのZERO点の設定です。
ZERO点をMach3に定義しておかないと、エンドミルの長さが変わった場合に正しく切削できなくなるからです。
写真の物はエンドミルが加工物に接触した時の導通でZERO点を検知するものです。
木材などの絶縁体とのZERO点を設定するために、金属プレートを対象物に乗せてそこにエンドミルが接触することでZERO点を認識します。
当然、プレートの厚み分高さが変わるのでプログラム内で相殺するように設定しています。
海外のCNC人が作っていたプログラムで、自動計測できるものがあったのでリクエストしたらプログラムを送ってくれました。
上のビデオ内で紹介していますが、ZERO点で”Tool ZERO Complete” とアナウンスしてくれる様になり、便利に使用しています。
ワニ口クリップはエンドミルに挟みます。タッチプレートの厚みは19.8mmなので、プログラム内でその分を相殺するわけです。 |
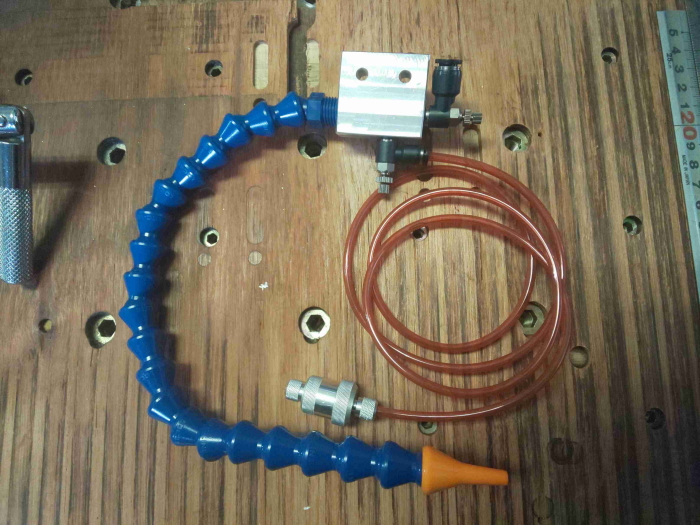 |
この様な物を自作しました。
青いジャバラノズルとコントロールバルブ付きフィッティングのみ購入し、他は
作業場の在庫をまさぐって出てきたもので組み上げました
アルミのボディーは、7075のブロックを切り出してフェースミルで6面を切削して
仕上げ、各部に穴あけ加工をしてタップを立てて完成です。
これはエアーを切削中のエンドミルに吹き付けて冷却を行うもので、ベンチュリー効果で
水タンクから水を吸い上げて細かなミストを発生させ、その気化熱でエンドミルを冷却
するものです。
購入するとそれなりの値段がするので、構造が簡単なので部品だけ安くそろえて金属部分だけ
自作するとコストが下げられます。 |
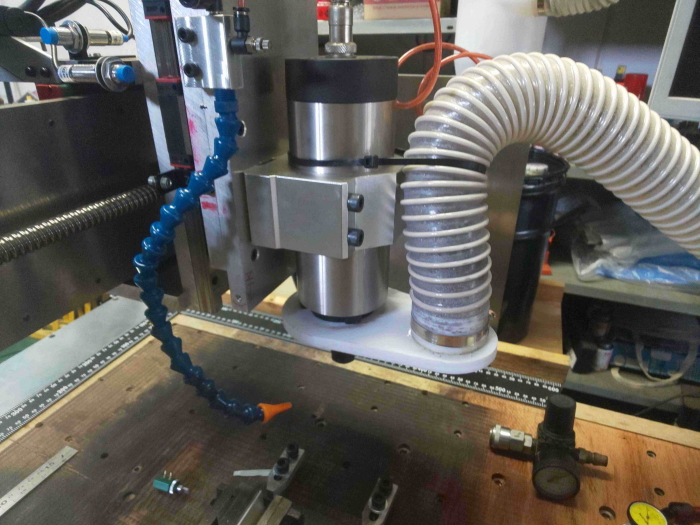 |
この様な取り付け方になります。コンプレッサーからエアーを送り、水通路のバルブを開くと
水ミストが発生して手を当てると冷えているのが感じられます。
これで切削中のエンドミルの温度が下げられそうです。
水しか使用しないので蒸発した後は他のクーラントに比べて、テーブルを汚さないので
掃除が楽でよいです。 |
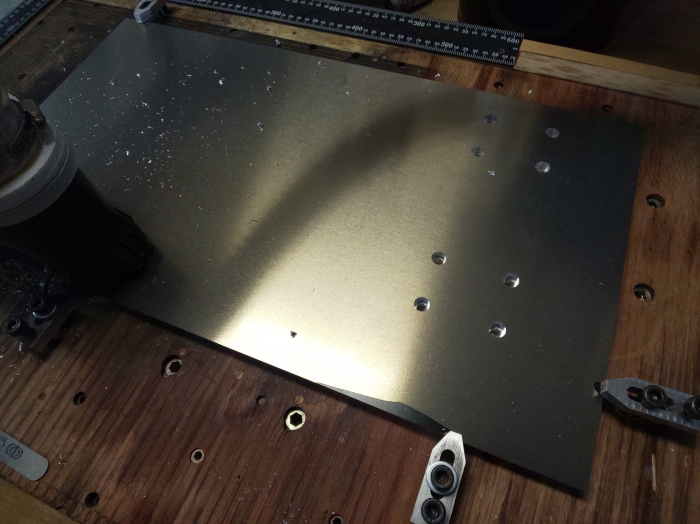 |
かねてよりの懸案だったガントリーの両サイドのプレートを
新しいデザインの物に変更するために切削中のカット。
8個の穴はキャップボルトが沈むポケットの切削が終わったところ。
材料はAL2024 15t を使用している。
|
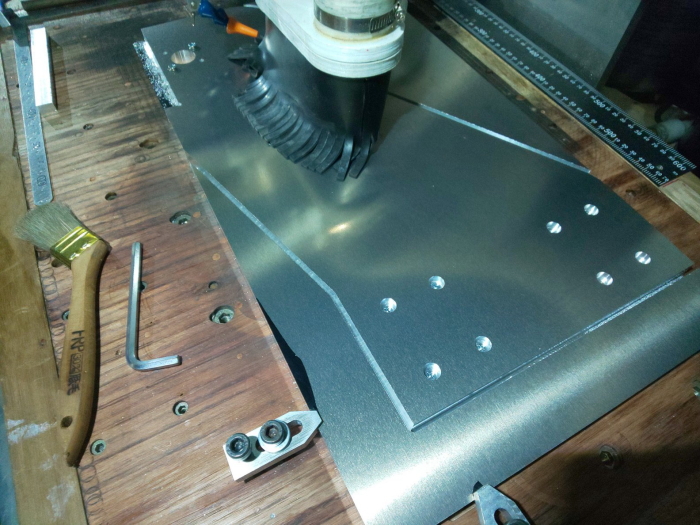 |
アウトラインをカット中の図 |
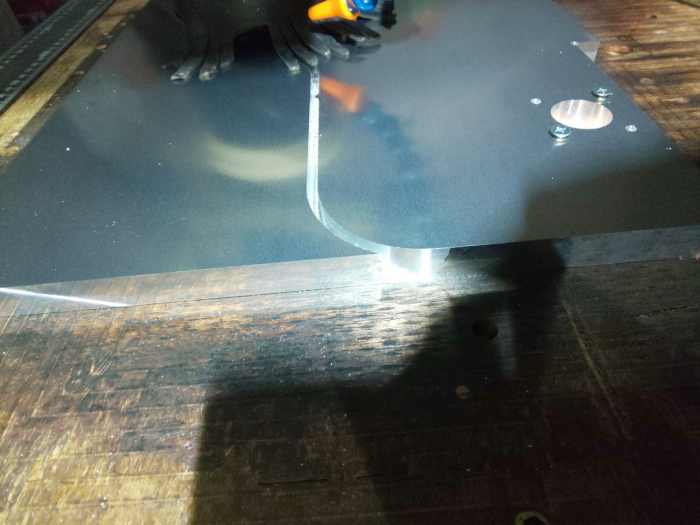 |
この様な感じで分厚い15tのアルミ板をカットしています。
ドライ切削で、バキュームが見事に切削粉を吸い込んでいるのが判ります。
切削中もほとんど削りカスが出ないので、テーブルがキレイに保てられます。
|
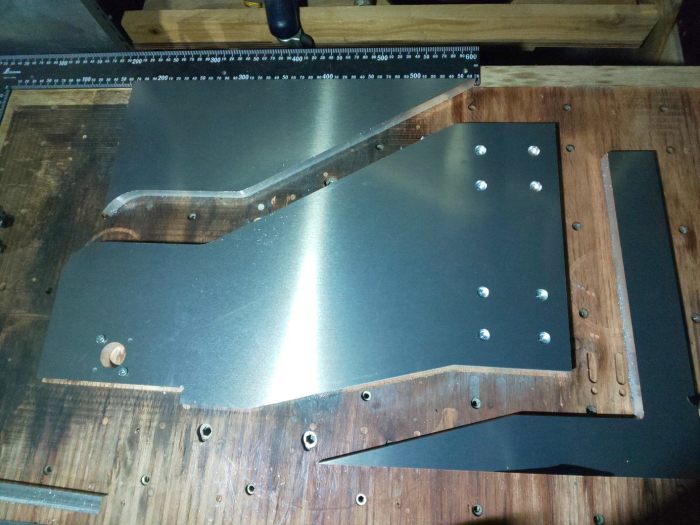 |
板から切り出された状態のサイドプレート。 |
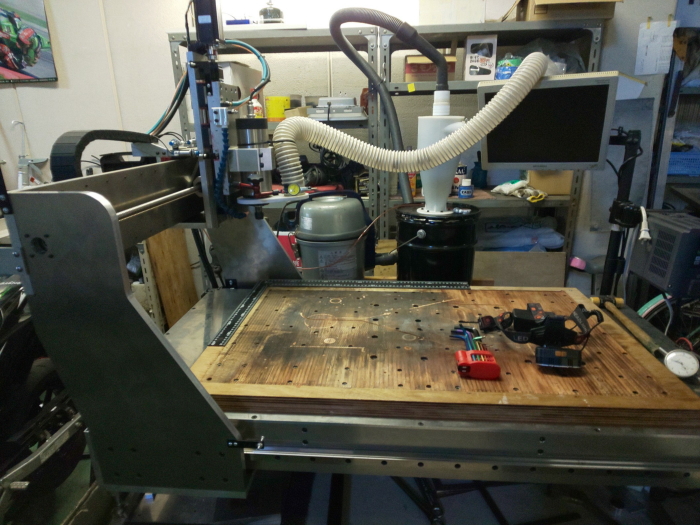 |
切り出したプレートを組み込んで完成。
初期の単板のままよりもワークテーブルへのアクセスが楽になりました。 |
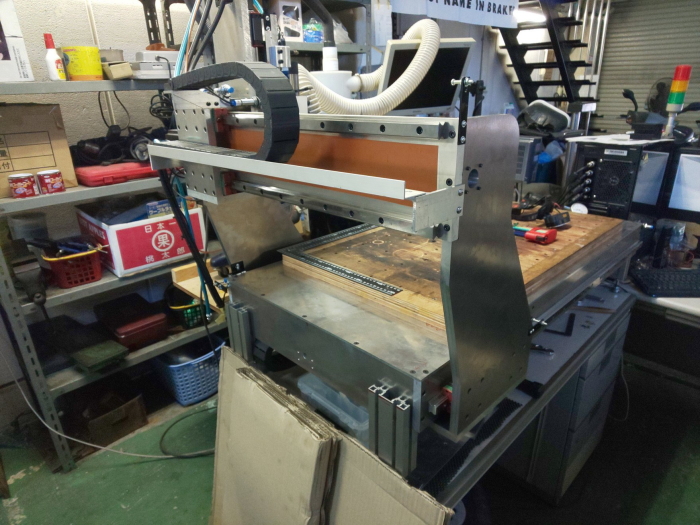 |
各軸の直角とセンター出しも終わり完璧な状態で次の仕事まで待機。
仕事の合間の時間でパーツを切り出すので自機の進化は時間が掛かりました。 |
|
2022/05/23
新しく3ページ目を追加しました
3ページ目へ!
|